Shrnutí:
V této studii byla představena metoda čištění radiální krystalizací za indukce pro výrobu 6N, 7N očkovacích krystalů s ultravysokou čistotou. Byl zkoumán vliv teploty chlazení na morfologii očkovacích krystalů, jakož i teplota chladicí vody, průtok a množství přidaného osiva do procesu krystalizace a nejlepší parametry procesu čištění byly získány následovně: teplota přípravy očkovacích krystalů: 278 K; Teplota a průtok chladicí vody 293 K a 40 L · h-1; a počet přidaných semen šest.
Byly zkoumány účinky teploty a průtoku chladicí vody na rychlost krystalizace. Rychlost krystalizace lineárně klesala se zvyšující se teplotou chladicí vody, ale rostla exponenciálně se zvyšujícím se průtokem chladicí vody. Příslušná rovnice pro rychlost krystalizace byla stanovena experimentálně a byla navržena tři schémata čištění. Když bylo surové gallium 4 N purifikováno podle schématu I, bylo získáno gallium s vysokou čistotou 6 N a gallium s vysokou čistotou 7 N podle schémat II a III. Čistota gallia o vysoké čistotě produkovaného třemi schématy I, II a III byla 99,999987%, 99,9999958% a 99,9999958%.
1. úvod
V 1970. letech bylo zjištěno, že sloučeniny obsahující prvky galium a skupiny IIIA měly vynikající polovodičové vlastnosti. Od té doby se galium (Ga) postupně používá jako surovina v polovodičovém průmyslu. V posledních letech, s neustálým rozvojem vědy a techniky a snahou lidí o nízkouhlíkovou ekonomiku a zelenou energii, byla aplikace Ga plně vyvinuta a stala se jednou z nejdůležitějších surovin v oblasti moderních polovodičů (asi 80% celkové spotřeby gália), solární energie (asi 10% celkové spotřeby gália), magnetické materiály (~ 5% celkové spotřeby gália) a katalyzátory a široce se používají v obraně, komunikaci optickými vlákny, letectví a dalších oblastech. V současné době je technologie výroby nízko kvalitního gália (čistota ≤ 99,99%) zdokonalována každý den. Statistiky amerického geologického průzkumu (USGS) z roku 2018 ukazují, že celosvětově činilo množství primární produkce nízkého gália v roce 2017 ~ 315 tun, což je nárůst o 15% oproti 2016 tunám v roce 274. Poptávka po galiu o vysoké čistotě vzrostla s vývojem vysoce výkonných polovodičových součástek, protože v proudu jsou přítomna i velmi malá množství nečistot, jako jsou Cu, Pb, Fe, Mg, Zn a Cr, velké komerční galium může degradovat nebo degradovat elektrické vlastnosti omezit. Byly použity běžné metody čištění, jako je elektrolytické čištění, regionální tavení, vakuová destilace a metoda tahání monokrystalů.
Pro výrobu gallia o vysoké čistotě je elektrolytický rafinační proces v současné době nejrozšířenější technologií v oboru výroby gallia o vysoké čistotě. Tyto tradiční metody však měly mnoho problémů, jako je vysoká spotřeba energie, nedostatek šetrnosti k životnímu prostředí, nízká účinnost výroby a nepříjemné řízení automatizace. Vývoj pokročilých technologií čištění je proto velmi důležitý pro rozvoj dnešního polovodičového a solárního průmyslu. Čištění a rafinace gallia jsme systematicky zkoumali. Na základě konvenční krystalizační metody byl navržen způsob výroby krystalizačních krystalů indukovaných krystalizací pomocí zárodečných krystalů. Tento proces má výhody nízké spotřeby energie, jednoduchého vybavení, pohodlného ovládání a krátkého výrobního cyklu. V této studii byl experiment krystalizace použit ke zkoumání vlivu teploty chlazení na morfologii krystalu a vlivu teploty chladicí vody, průtoku a množství očkovacího krystalu přidaného v procesu krystalizace. Parametry čisticího procesu byly studovány za účelem optimalizace nejlepšího čisticího procesu, stanovení rovnice řízení rychlosti krystalizace a vytvoření kovového gallia o vysoké čistotě (6N a 7N) za podmínek procesu.
2. Materiály a metody
2.1. Návrh procesu Obrázek 1 ukazuje výrobní proces čisticího procesu bicyklických krystalů krystalického gallia s vysokou čistotou 6N, 7N indukcí semen. Hlavní kroky a postupy jsou následující: (1) Čištění krystalizátoru a montáž čističe Nejprve byl krystalizátor propláchnut vysoce čistou vodou (odpor> 16 MΩ · cm), aby se odstranil prach na povrchu. Poté byl čištěn pomocí ultrazvukového čističe obsahujícího ultračistou vodu po dobu 2 hodin, aby se odstranily zbytkové nečistoty na povrchu. Čisticí zařízení bylo sestaveno tak, jak je znázorněno v 1b. (2) Předúprava surového gallia 4 N. Surové gallium 4 N bylo umístěno na varnou desku společně s balicí lahví a teplota zahřívání byla nastavena na 335 K. Po roztavení gallia bylo roztavené surové gallium přeneseno do polytetrafluorethylenové kádinky a smícháno s 200 ml 3 mol / l HCI při 335 K po dobu 2 hodin. Kyselina chlorovodíková byla odsáta plastovou pipetou a poté bylo přidáno 200 ml 3 mol / l HNO3. přidá se do kádinky, následuje míchání a míchání po dobu 2 hodin. Surové gallium se promylo kyselinou a následně třikrát promývalo ultračistou vodou. Kyselina chlorovodíková a kyselina dusičná použité při zpracování kyselinou byly vysoce čisté a k přípravě kyselého roztoku byla použita ultračistá voda. Předupravené roztavené surové gallium (4N) bylo převedeno do čistého krystalizátoru. Cirkulační chladicí voda byla zavedena do vodního pláště krystalizátoru. Chladicí voda byla dodávána pomocí vodní nádrže s nízkou konstantní teplotou a zabudovaného cirkulačního čerpadla. Teplotní rozsah byl mezi 263 a 373 K, přesnost regulace teploty byla ± 0,1 K a průtok chladicí vody byl řízen průtokoměrem se skleněným rotorem. Když teplota kapalného gália poklesla na kritický bod krystalizace, byla přidána krystalová semena a cirkulační chladicí voda. Tyto krystaly byly připraveny s použitím gallia 7N jako suroviny pro zahájení purifikačního testu. Použitý postup je následující: Polytetrafluorethylenový kelímek obsahující roztavený gallium 7N byl uveden do nízké konstantní teploty, aby ochladil a krystalizoval vodu. Tekuté gallium se nepřetržitě míchalo teflonovou tyčí, aby se dispergovalo jádro krystalu a zvýšila se rychlost nukleace. Během procesu míchání byla pozorována krystalizace kapalného gallia.
Přepnul se třícestný spínač a cirkulační horká voda byla zavedena do chladicí / tavicí zóny krystalizátoru. Po úplném roztavení pevného gália se třícestný spínač přepnul a cirkulační chladicí voda se znovu zavedla do chladicí / tavicí zóny; Teplá voda byla dodávána pomocí nádrže na vodu s konstantní teplotou a vestavěného oběhového čerpadla. Teplotní rozsah byl 278–373 K a přesnost regulace teploty byla ± 1 K. Kroky (jak je znázorněno na obrázku 1c) se opakovaly až do stanoveného počtu krystalizací. Po dokončení čištění byla stanovena kvalita produktu.
Byl přepnut třícestný přepínač a cirkulující horká voda byla zavedena do chladicí / tavicí zóny krystalizátoru. Po úplném roztavení pevného gallia se přepnul třícestný přepínač a cirkulační chladicí voda byla znovu zavedena do chladicí / tavicí zóny; Horká voda byla dodávána pomocí nádrže na vodu s konstantní teplotou a zabudovaného cirkulačního čerpadla. Teplotní rozsah byl 278-373 K a přesnost regulace teploty byla ± 1 K.
Kroky (jak je znázorněno na obrázku 1c) byly opakovány až do předem stanoveného počtu krystalizací. Po dokončení čištění byla stanovena kvalita produktu.
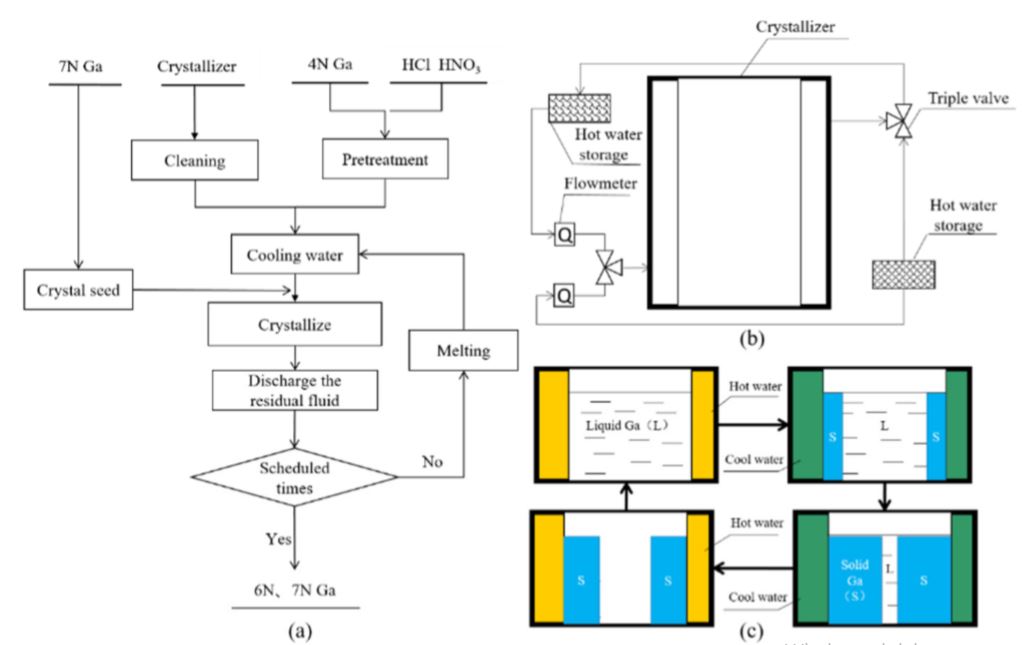
Obrázek 1. Schematické znázornění čisticího procesu: a) postupnost procesu čištění, b) montáž čisticího zařízení a c) opakovaný krystalizační proces.
2.2. detekční metody
V experimentu byly obsahy nečistot 4N galliové suroviny a čištěného 6N, 7N gallium detekovány pomocí hmotnostní spektrometrie s výbojovou žárovou výbojkou (Evans Materials Technology (Shanghai) Co., Čína, HR-GDMS)) a čistota produktu byla stanovena diferenční metodou vypočítat. Jako detekční plyn byl použit Argon. Parametry hmotnostní spektrometrie jsou následující: vybíjecí proud 1,9 mA; Vybíjecí napětí 1 kV; Proud paprsku iontů gallia 1 × 10-6 mA; Izolační vrstva, hliník; a rozlišení ≥ 3600. Před získáním dat byl zdroj iontů HR-GDMS ochlazen na teplotu kapalného dusíku (90 K), aby se snížilo rušení iontů v plynném pozadí. Poté byl povrch testovaného vzorku (0,2 x 2 mm 2) rozprašován po dobu 5 minut při teplotě kapalného dusíku, aby se odstranily kontaminanty z povrchu vzorku. Podmínky před rozprašováním byly udržovány konstantní a byl zahájen sběr dat. Během procesu sběru dat byl integrační čas nastaven na 80 ms.
3. Výsledky a diskuse
3.1. Vliv chladicí teploty na morfologii semen
Morfologie vzhledu očkovacího krystalu produkovaného při teplotě chlazení v rozmezí 265-295 K je znázorněna na obrázku 2. To ukazuje, že ztuhlá struktura v 265 K obsahovala mnoho zrn jemných krystalů a zrna byla rozptýlena s velkým množstvím tekutého gallia. Když byla ztuhlá struktura odstraněna, na povrch bylo navázáno velké množství tekutého gallia, což mělo za následek extrémně nepravidelný tvar semene, protože v 265 K se rychlost růstu jádra krystalu po nukleace zvýšila kvůli vysokému stupni podchlazení, což vedlo k vytvoření jádra krystalu velké množství dendritů vede. Rychlý růst dendritů se nejen mísí s velkým množstvím kapalné fáze uvnitř ztuhlé struktury, ale také způsobuje hodně dutého povrchu ztuhlé struktury. Při teplotě přípravy 273 K vykazovala solidifikovaná struktura geometrické polyhedrální tvarové znaky, což naznačuje, že se snížením stupně podchlazení se snížila rychlost růstu jádra krystalu a jeho růstový režim se změnil z dendritového na lamelární růst. Když byla produkční teplota 278 K, solidifikovaná struktura vykazovala pravidelný hexahedrální tvar, což naznačuje, že se zvyšující se teplotou klesal stupeň podchlazení růstové fronty po vytvoření jádra krystalu a růstový režim se změnil, pokud jde o růst ve vrstvách. Při přípravné teplotě 295 K se stupeň podchlazení rozhraní pevná látka-kapalina dále snížil po vytvoření jádra krystalu, což brání uvolnění latentního tepla z krystalizace. V této době se směr růstu krystalového jádra změnil na postranní růst a zkreslil jeho geometrický tvar, aby rychleji uvolnil latentní teplo krystalizace. Porovnáním morfologických vlastností semen produkovaných při čtyřech teplotách byla nakonec stanovena optimální teplota produkce semen 278 K. Při výrobní teplotě 273 K vykazovala ztuhlá struktura geometrické polyedrické tvary, což naznačuje, že se snížením stupně podchlazení se snížila rychlost růstu krystalového jádra a jeho růstový režim se změnil z růstu dendritu na růst lamel. Když byla produkční teplota 278 K, solidifikovaná struktura vykazovala pravidelný hexahedrální tvar, což naznačuje, že se zvyšující se teplotou klesal stupeň podchlazení růstové fronty po vytvoření jádra krystalu a růstový režim se změnil na růst vertikální vrstvy. Při přípravné teplotě 295 K se stupeň podchlazení rozhraní pevná látka-kapalina dále snížil po vytvoření jádra krystalu, což brání uvolnění latentního tepla z krystalizace. V této době se směr růstu krystalového jádra změnil na postranní růst a zkreslil jeho geometrický tvar, aby rychleji uvolnil latentní teplo krystalizace.
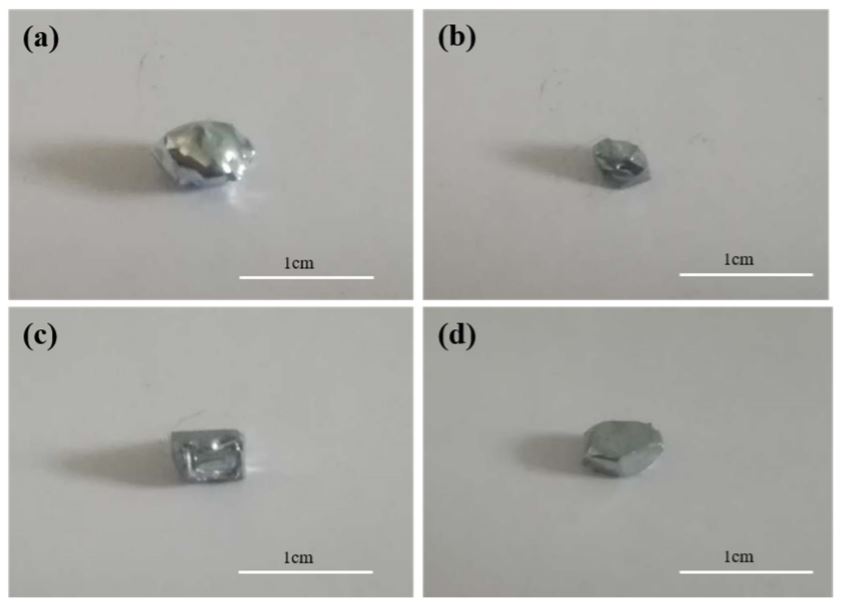
Obrázek 2. Morfologie očkovacích krystalů připravených při různých chladicích teplotách (a) 265 K, (b) 273 K, (c) 278 K a (d) 295 K).
3.2. Vliv parametrů procesu na krystalizační proces
3.2.1. Vliv teploty chladicí vody na krystalizační proces
Když byla průtoková rychlost chladicí vody 40 L · h-1 a teplota byla v rozmezí 288-298 K, bylo 2,9774 kg surového gallia předběžně ošetřeného mořením ochlazeno na kritický bod krystalizace a následně bylo přidáno očkování pro 15 minuta Odpovídající morfologie růstu krystalů je znázorněna na obrázku 3.
Obrázek 3 ukazuje, že když teplota chladicí vody byla 288 a 290 K, byl růstový režim tekutých galliových krystalů hlavně růstem dendritů po přidání zárodečných krystalů a větve krystalů byly navzájem přemostěny, přičemž kapalné gallium bylo zachyceno v krystalu. Bylo to proto, že při nižší teplotě chladicí vody byl teplotní gradient uvnitř kapalného galia vyšší a rychlost růstu krystalu po přidání zárodečného krystalu byla rychlejší. Ačkoli byl v této době vytvořen pozitivní teplotní gradient, teplota na rozhraní rozhraní pevná látka-kapalina v radiálním směru krystalizátoru byla vyšší, což bránilo uvolňování latentního tepla krystalizace v tomto směru, a tím snížilo růst krystalu v tomto směru. Aby se však usnadnilo uvolňování latentního tepla krystalizace, změnila se růstová orientace krystalu a rychle rostla ve formě dendritů, což nakonec narušilo větve krystalu a přemostilo se
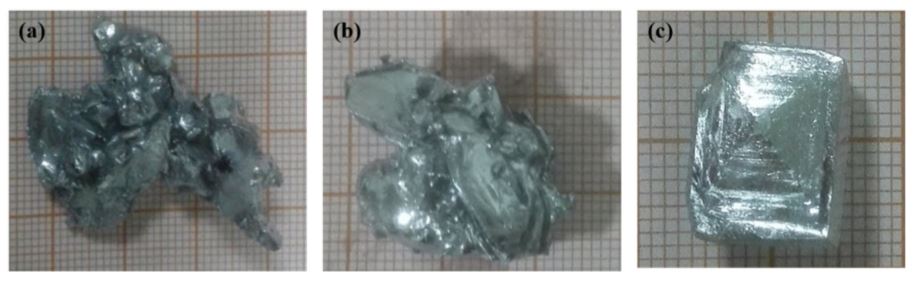
Obrázek 3. Krystalická morfologie tekutého gallia po 15minutovém přidání jader při různých teplotách chladicí vody ((a) 288 K, (b) 290 K a (c) 293 K).
Zahrnutí kapalné fáze.
Unášené kontaminanty kapalné fáze nemohou být odstraněny kvůli růstu krystalů, což ovlivňuje proces čištění. Když byla teplota chladicí vody 293 K, kapalné gallium po přidání očkovacích krystalů vzrostlo na monokrystal.
Aby se dále analyzovala zákon růstu tekutého gallia během krystalizace, byla morfologie krystalu zkoumána v různých časech po přidání jádra krystalu metodou dynamického měření času při proudu chladicí vody 40 L · h-1 a teplotě 293 K. Výsledek je znázorněno na obrázku 4.
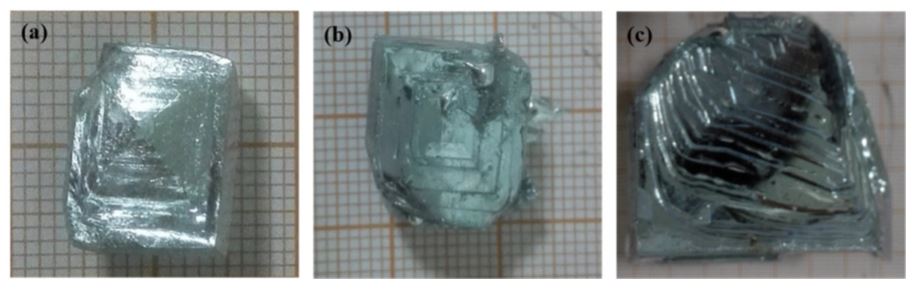
Obrázek 4. Morfologické obrazy krystalických bloků v různých časech po přidání semene ((a) 15 min, (b) 30 min a (c) 60 min).
Obr. 4 ukazuje, že po přidání zárodku se ingot galliového krystalu postupně zvyšoval se zvyšující se dobou krystalizace a režim růstu tekutého galliového krystalu po přidání zárodečných krystalů vykazoval typický vrstevnatý růst střihu indikující teplotu. z růstu krystalů vytvořilo latentní teplo krystalizace na přední stranu rozhraní pevná látka-kapalina a přeneslo a uvolnilo je ve směru teplotního gradientu směrem ven. Tento typ růstu krystalových vrstev byl výhodný pro akumulaci nečistotních prvků z rozhraní pevná látka-kapalina do kapalné fáze, čímž se získal kov s vyšším obsahem Ga. Stupeň podchlazení růstového píku byl největší, když krystal rostl, a atomy kapalného gallia na rozhraní pevná látka-kapalina byly přednostně vázány na růstový pík a teplo bylo přeneseno ven z krystalizovaného pevného galia do pozitivního teplotního gradientu v krystalizátoru. , Proto růst krystalů v procesu krystalizace vždy probíhal ve formě pyramidálního postupného postupu. Podle kinetiky a termodynamiky růstu krystalů se ukázalo, že vrstvený růst napomáhá zvětšení povrchové plochy krystalů, usnadňuje uvolňování latentního tepla krystalizace a zajišťuje kontinuální a stálý růst krystalů během procesu krystalizace. Kromě toho lze podle teorie separace a koagulace předpokládat nečistoty v krystalu
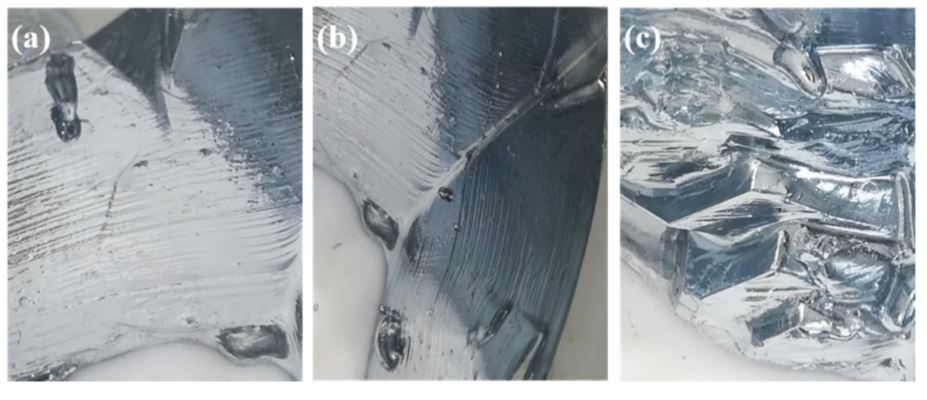
Obrázek 5. (a) Pro 30 L · h · 1 v blízkosti výstupu z krystalizátoru, (b) pro 40 L · h · 1 v blízkosti vstupu do krystalizátoru a (c) pro 50 L · h · 1, podrobná morfologie krystalu galia v blízkosti vstupu krystalizátoru krystalizátoru čistý průchod.
Obohacení nečistotních prvků z hranice pevná látka-kapalina do kapalného stavu a zamezení nečistot obálkami v kapalné fázi v důsledku nepravidelného směru růstu krystalů. 4 ukazuje, že se zvyšující se dobou krystalizace se pyramidová špička krystalu stala viditelnější a krok vrstvení růstu krystalů se stal zřejmějším, když krystalizace pokračovala, nečistotní prvky se neustále akumulovaly v kapalné fázi a čistota se zvyšovala na rozhraní pevná látka-kapalina. co přilnavost rozhraní pevná látka-kapalina zlepšilo pík růstu krystalu. Kvůli rozdílu v atomovém poloměru a elektronegativitě mezi Ga a elementy nečistoty napadly atomy nečistot připojené k píku růstu Ga mříž nebo volné místo mřížky a způsobily vadu růstu krystalu Ga. To ukázalo, že odstraňování nečistotních prvků klesalo s postupem krystalizace a shodovalo se s údaji z literatury.
3.2.2. Vliv proudu chladicí vody na krystalizační proces
V předchozí studii byl zkoumán především vliv proudu chladicí vody na krystalizační proces. Výsledky ukázaly, že rychlost růstu krystalu gallia v blízkosti výstupu z krystalizátoru byla o něco nižší než v jiných oblastech, když průtoková rychlost chladicí vody byla 30 LH-1. Když byla průtoková rychlost chladicí vody 50 · H - 1, byla rychlost růstu krystalu galia ve spodní části krystalizátoru o něco větší než rychlost v horní části a rychlost růstu v blízkosti vstupu krystalizátoru byla největší. Při průtokové rychlosti chladicí vody 40 L · h-1 byla rychlost růstu krystalů gallia ve všech oblastech krystalizátoru v podstatě stejná a žádný fenomén místního růstu nebyl pozorován příliš rychle nebo příliš pomalu. Pro další zkoumání účinku tohoto parametru procesu na krystalizační proces byla pozorována krystalová morfologie kapalného gallia při různých proudech chladicí vody. Výsledky jsou uvedeny na obrázku 5.
To je přičítáno skutečnosti, že s postupující krystalizací se kontaminanty kontinuálně akumulovaly v kapalné fázi a obsah nečistot na rozhraní pevná látka-kapalina se zvyšoval, což zvyšuje pravděpodobnost, že se kontaminující prvky připojí k píku růstu krystalu. Kvůli rozdílu v atomovém poloměru a elektronegativitě mezi Ga a elementy nečistoty napadly atomy nečistot připojené k píku růstu Ga mříž nebo volné místo mřížky a způsobily vadu růstu krystalu Ga. To ukazuje, že odstraňování nečistotních prvků s postupující krystalizací klesá a odpovídá údajům z literatury.
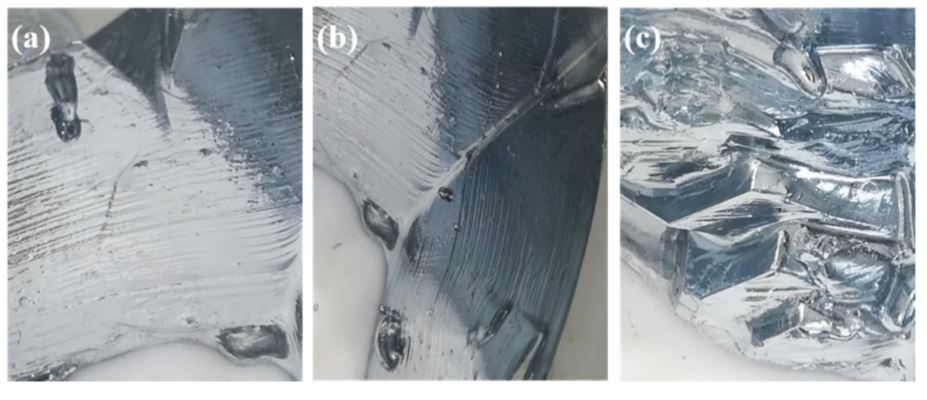
Obrázek 5. (a) Pro 30 L · h · 1 v blízkosti výstupu z krystalizátoru, (b) pro 40 L · h · 1 v blízkosti vstupu do krystalizátoru a (c) pro 50 L · h · 1, podrobná morfologie krystalu galia v blízkosti vstupu krystalizátoru krystalizátoru čistý průchod.
Obrázek 5 ukazuje, že krystalická morfologie gália s průtokem chladicí vody 40 l · h - 1 ukázala jasný „vzor skořápky“ s rovnoměrným roztečem zrn. To naznačovalo, že krystal gália rostl vrstvu po vrstvě při této rychlosti toku a byl prospěšný při odstraňování kontaminace. Při průtoku chladicí vody 30 L · h - 1 byla rychlost růstu krystalů na výstupní straně krystalizátoru o něco pomalejší než v jiných oblastech a morfologie krystalů byla stejná jako u průtoku chladicí vody 40 L · h - 1, přičemž se také zobrazuje odlišný „vzor mísy“ . To naznačuje, že za těchto podmínek toku krystaly gália také rostly vrstvu po vrstvě, což bylo přínosné pro odstraňování nečistot; Rychlost růstu krystalů zde však byla pomalejší než v okolní oblasti, takže v tomto okamžiku nelze vyloučit možnost obalení kapalné fáze v průběhu krystalizace. S výkonem chladicí vody
Růst krystalů byl větší a rychlost růstu krystalů byla rychlejší, což změnilo morfologii krystalu a přítomnost velkého počtu nepravidelných růstových kroků. Z toho lze usoudit, že krystaly v místě nerostou úplně ve vrstvách, a proces růstu krystalů může být doprovázen dendritem nebo peritektickou tvorbou, což vede k fázi kapalné skořápky, včetně nečistot a snížení pevného čištění galliem.
3.2.3. Vliv počtu zárodků na krystalizační proces
S proudem chladicí vody 40 lh-1 a teplotou 293 K bylo přidáno kapalné gallium ochlazené na kritický bod krystalizace a byly přidány zárodečné krystaly 3, 4, 5 a 6. Když krystalizace dosáhne určité úrovně, její morfologický obraz je zobrazen v 6, což naznačuje, že počet přidaných semen určuje tvar nekrystalizované oblasti. Když byly přidány tři očkovací krystaly, nekrystalizovaná oblast měla trojúhelníkový tvar. Když byla přidána čtyři jádra, nekrystalizovaná oblast měla rovnostranný tvar. Když však byl počet přidaných jader krystalu 3 nebo 4, tvar a velikost nekrystalizované oblasti se neshodovaly a vykazovaly tvar trychtýře s velkým vrcholem a malým dnem. To snadno vedlo k průniku růstu krystalů ve spodní části krystalizátoru s kontinuálním průběhem krystalizace, který způsobil vývoj kapalné fáze a začlenění nečistot, což ovlivnilo účinek deflagrace. Když bylo přidáno pět očkovacích krystalů, nekrystalizovaná oblast vykázala pětiúhelníkový tvar a problém s tvarem s velkou horní a malou spodní částí v nekrystalizované oblasti se zlepšil. V případě přidání šesti očkovacích krystalů nekrystalizovaná oblast vykazovala hexagonální tvar pravidelného tvaru a jednotné velikosti a byla nejvýhodnější pro řízení celkového směru krystalu během čištění surového gallia. Proto byl optimální počet přídavků semen stanoven na šest, když bylo surové gallium 4 N purifikováno pomocí krystalizátoru vyrobeného samotným způsobem.
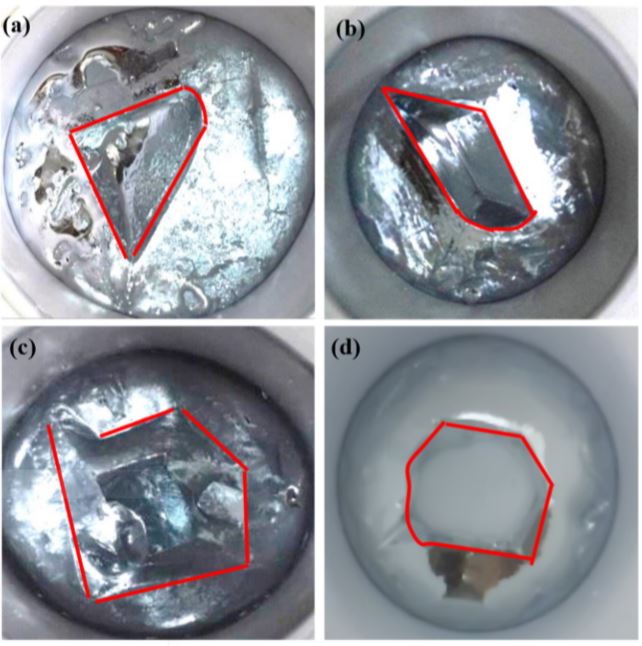
Obrázek 6. Fotografie krystalové morfologie s přidáním různého počtu jader ((a) 3, (b) 4, (c) 5 a (d) 6).
3.3. Vliv parametrů procesu
3.3. Vliv parametrů procesu na rychlost krystalizace
Ve skutečném procesu tuhnutí krystalizace kapalného gallia rychlost krystalizace (tj. Rychlost růstu krystalů gallia po přidání jader) závisí na stupni podchlazení rozhraní pevná látka-kapalina. Stupeň podchlazení rozhraní pevná látka-kapalina byla funkcí teploty a průtoku chladicí vody, aby se udržely konstantní další podmínky procesu. V experimentu byly vztahy mezi rychlostí krystalizace a teplotou chladicí vody a průtokem měřeny metodou regulačních proměnných a empirický regulační vzorec rychlosti krystalizace byl získán analýzou experimentálních dat. Za účelem snížení experimentální chyby, zlepšení přesnosti empirického kontrolního vzorce a jeho adaptability na skutečný výrobní proces byla každá skupina experimentů měření opakována čtyřikrát a byl vytvořen průměr. Rychlost krystalizace měřená v experimentu byla změněna během kompletního procesu tuhnutí tekutého gallia po přidání semene a výpočetní vzorec je následující:
v = m / t
kde v je průměrná rychlost, kg / h; m je celková hmotnost kapalného galia, kg; t je doba potřebná pro úplné ztuhnutí tekutého galia, hodina (h). Vliv teploty a průtoku chladicí vody na rychlost krystalizace stanovenou zkouškou je uveden v 7. 7a ukazuje, že se zvyšující se teplotou chladicí vody se rychlost krystalizace postupně snižuje a je mezi nimi pozorován zřejmý lineární vztah. Empirický kontrolní vzorec teploty chladicí vody pro rychlost krystalizace byl získán přizpůsobením softwaru Origin.
v (T) = -0,09 T + 27
kde T je teplota chladicí vody K; a koeficient lineární korelace přizpůsobení dat byl R2 = 0,997. 7b ukazuje, že jak se zvyšuje průtok chladicí vody, zvyšuje se rychlost krystalizace a mezi nimi se pozoruje významný exponenciální funkční vztah. Empirický kontrolní vzorec proudění chladicí vody do rychlosti krystalizace byl získán pomocí softwaru Origin software.
v (Q) = -96,73e - Q 4,94 + 0,66
kde Q je průtok chladicí vody, L / h; a standardní odchylka přizpůsobení dat byla R2 = 0,997.
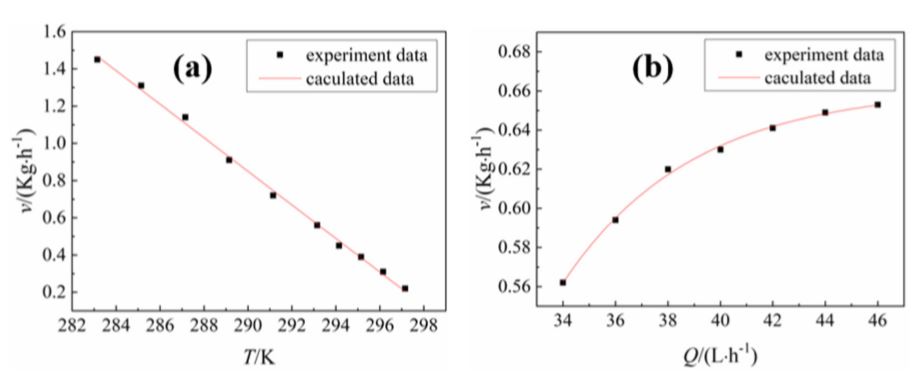
Obrázek 7. (a) Vliv teploty chladicí vody na rychlost krystalizace při průtoku 40 L · h-1; (b) Vliv průtoku chladicí vody na rychlost krystalizace v 293 K.
3.4. Analýza výsledků čištění
Na základě výše uvedených výzkumů byly stanoveny optimální technologické parametry pro čištění krystalů 4N surové suroviny gallium následujícím způsobem: Teplota přípravy osiva, 278 K; Teplota chladicí vody, 293 K, průtok chladicí vody, 40 L · h-1, a počet přidaných očkovacích krystalů byl šest. V kombinaci s naším předchozím výzkumem byly vytvořeny tři schémata čištění
Hladiny nečistot v galliu o vysoké čistotě připravené třemi purifikačními schématy byly testovány a porovnány se surovinou gallia a byla vypočtena rychlost odstranění nečistot. Výsledky jsou uvedeny v tabulce 2.
Tabulka 2 ukazuje, že po čištění byly frakce nečistot obsažené v materiálech sníženy pod detekční limit HR-GDMS a dalších šest hlavních nečistot bylo také dobře odstraněno. Rychlosti odstraňování byly: Fe-87,1%, Pb-95,9%, Zn-89,9%, Mg-97,9%, Cu-98,8% a Cr-93,3% a hmotnostní podíl hliníkového kovu vypočtený diferenční metodou byl 99,999987%.
Ve schématu II byly rychlosti odstraňování šesti hlavních nečistot Fe-93,8%, Pb-98,8%, Zn-95,6%, Mg-99,6%, Cu-99,8% a Cr-97,6% a hmotnostní frakce hlavního Ga kovu byla 99,9999958% , Ve schématu III se rychlost odstraňování šesti hlavních nečistot dále zvyšovala a rychlost odstraňování Mg a Cu překročila 99,9%. Naproti tomu rychlost odstranění Fe, i když nejnižší, dosáhla také 97%. Hmotnostní zlomek hlavního kovu Ga byl 99,9999958%.
4. závěry
Stručně řečeno, navrhuje se podrobně odstranit nečistotu zkoumaného Ga a provést krystalizační purifikační proces pomocí této krystalové indukce. Vliv teploty chlazení na morfologii krystalu a teplotu chladicí vody, průtok a počet jader přidaných do studovaného krystalizačního procesu. Byla získána optimální metoda čištění; byla stanovena kontrolní rovnice rychlosti krystalizace; a gallium o vysoké čistotě (6N a 7N) bylo vyrobeno za technologických podmínek. Hlavní závěry této studie jsou následující:
- Optimální parametry procesu pro krystalizační purifikaci surového materiálu gallia 4N jsou následující: teplota semenného přípravku 278 K; Teplota chladicí vody 293 K; Průtok chladicí vody 40 L · h - 1; počet očkovacích krystalů přidal šest 6;
- Rychlost krystalizace lineárně klesala se zvyšující se teplotou chladicí vody a zvyšovala se exponenciálně se zvyšujícím se tokem chladicí vody. Kontrolní vzorce teploty T chladicí vody a průtoku Q nad krystalizační rychlostí v jsou: v (T) = -0,09T + 27 a v (Q) = -96,73e -Q 4,94 + 0,66;
- Tři navrhovaná schémata čištění účinně odstranila kontaminující prvky. Při použití schématu I k čištění surového niklu 4 bylo získáno gallium o vysoké čistotě s čistotou 6 N. Za použití schémat II a III byl 7N dán galliu o vysoké čistotě. Čistota gallia o vysoké čistotě připraveného podle schémat I, II a III byla 99,999987%, 99,9999958% a 99,9999958%.
Metoda semenem indukované radiální krystalizace navržená ve studii nabízí výhody snadnosti provozu, pohodlného toku procesu, nízké spotřeby energie, šetrného k životnímu prostředí a snadno implementovatelného automatického řízení procesu čištění a poskytuje nový nápad pro průmyslovou výrobu gallia s vysokou čistotou ,
Ústav kovů vzácných zemin
Katedra chemie a chemického inženýrství, Lvliang University, Čína
Škola metalurgie, Northeastern University, Shenyang, Čína